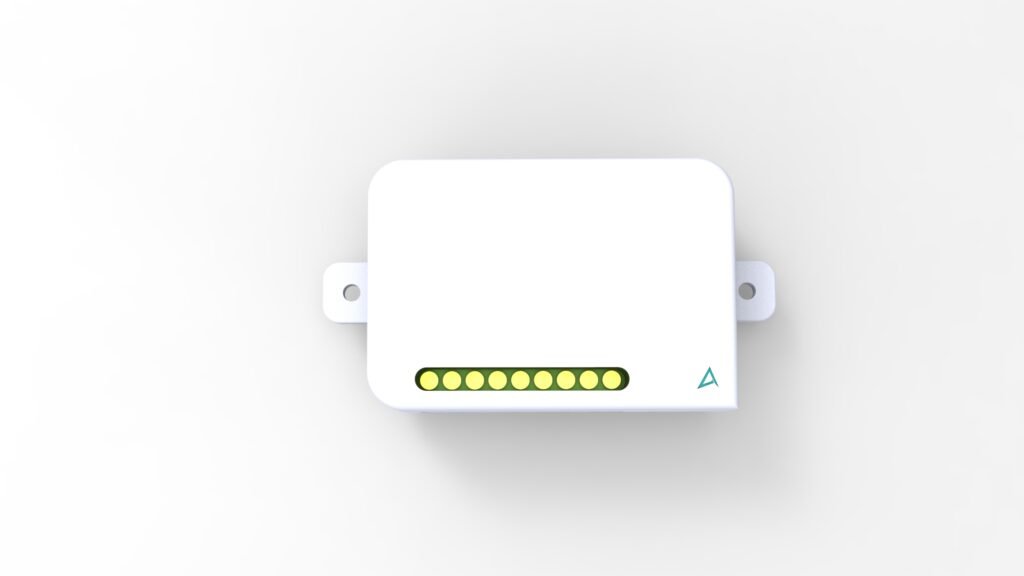
Level Controller
A level controller is an essential device used in industrial processes to maintain and control the level of liquids within a tank or vessel. It plays a crucial role in ensuring optimal fluid levels, preventing overflows, and maintaining consistent and safe operations in various industries, including chemical, pharmaceutical, water treatment, and manufacturing.
Key Components and Operation:
Sensing Element: The level controller is equipped with a sensing element that detects the liquid level within the tank. Different types of sensing elements may include floats, capacitance probes, ultrasonic sensors, or pressure sensors, depending on the specific requirements of the application.
Controller Unit: The controller unit processes the signals from the sensing element and activates control mechanisms to adjust the fluid level as needed. It can operate using different control strategies, such as on/off control or proportional-integral-derivative (PID) control.
Control Mechanism: The control mechanism is responsible for adjusting the flow of liquid into or out of the tank based on the signals received from the sensing element and the set point programmed in the controller. This can involve opening or closing valves, adjusting pump speed, or activating other fluid control devices.
Types of Level Controllers:
On/Off Level Controllers: These controllers operate by turning the filling or draining mechanism on or off based on the level sensor’s readings. They are suitable for applications where precise control is not critical.
Proportional Level Controllers: Proportional controllers modulate the control valve or pump in proportion to the difference between the actual and desired levels. This provides more precise control and helps maintain a stable level.
PID Level Controllers: PID controllers combine proportional, integral, and derivative control actions to improve the responsiveness and stability of the system. They are commonly used in applications where tight control over the level is necessary.
Applications:
Industrial Tanks: Level controllers are extensively used in tanks storing liquids or bulk materials, ensuring that the levels are within specified ranges. This is crucial for maintaining operational efficiency and preventing potential issues such as overflows.
Water Treatment Plants: In water treatment facilities, level controllers are employed to manage water levels in different treatment stages, optimizing processes and preventing disruptions.
Chemical Processing: Level controllers play a vital role in chemical manufacturing, helping maintain precise levels for mixing, reactions, and inventory control.
Oil and Gas Industry: Level controllers are used in storage tanks, pipelines, and processing units within the oil and gas sector to monitor and control fluid levels, preventing spillages and ensuring safety.
Benefits:
Prevention of Overflows: Level controllers prevent overflows by automatically adjusting the inflow or outflow of liquids based on set parameters.
Process Optimization: Maintaining consistent fluid levels contributes to the efficient operation of industrial processes, ensuring that the right amount of material is available for production or treatment.
Safety: By preventing overflows and maintaining stable levels, level controllers contribute to a safer working environment, reducing the risk of accidents and spills.
In conclusion, level controllers are integral components in industrial processes where precise control over fluid levels is essential. Their diverse applications across industries contribute to operational efficiency, safety, and the prevention of potential hazards associated with inadequate level control.